Advanced Welding WPS: Tailoring Specifications for Facility Tasks
Advanced Welding WPS: Tailoring Specifications for Facility Tasks
Blog Article
Opening the Power of Welding WPS: Techniques for Efficiency and Safety And Security in Construction
In the realm of manufacture, Welding Procedure Requirements (WPS) stand as the backbone of welding procedures, determining the necessary steps for accomplishing both effectiveness and safety in the fabrication process. Comprehending the complexities of WPS is critical to harnessing its complete potential, yet lots of organizations battle to open the true power that exists within these records (welding WPS). By delving into the strategies that optimize welding WPS, a globe of improved efficiency and increased safety and security waits for those ready to discover the nuances of this essential aspect of fabrication

Relevance of Welding WPS
The value of Welding Procedure Requirements (WPS) in the manufacture sector can not be overemphasized. WPS work as an essential roadmap that outlines the necessary actions to guarantee welds are done regularly and appropriately. By specifying essential criteria such as welding processes, products, joint layouts, preheat temperatures, interpass temperatures, filler steels, and post-weld heat treatment requirements, WPS offer a standard approach to welding that enhances effectiveness, top quality, and security in fabrication procedures.
Adherence to WPS aids in accomplishing harmony in weld high quality, lowering the likelihood of flaws or architectural failures. This standardization likewise facilitates conformity with industry regulations and codes, ensuring that fabricated structures fulfill the called for security requirements. Moreover, WPS paperwork makes it possible for welders to duplicate successful welding treatments, causing consistent results throughout various tasks.
Fundamentally, the precise development and rigorous adherence to Welding Procedure Requirements are critical for upholding the honesty of welded frameworks, securing against potential hazards, and upholding the reputation of construction business for providing top notch products and solutions.
Crucial Element of Welding WPS
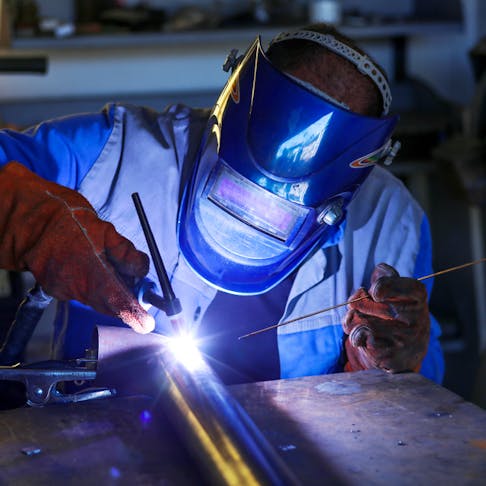
Enhancing Performance With WPS
When optimizing welding operations, leveraging the essential components laid out in Welding Procedure Specs (WPS) comes to be essential for enhancing processes and optimizing efficiency. One way to improve performance with WPS is by thoroughly picking the suitable welding criteria. By adhering to the certain standards offered in the WPS, welders can make certain that the welding equipment is view established appropriately, resulting in top notch and consistent welds. Furthermore, complying with the pre-approved welding sequences outlined in the WPS can dramatically decrease the time invested in each weld, inevitably increasing general efficiency.
Routinely assessing and updating the WPS to include any lessons discovered or technical developments can also add to effectiveness improvements in welding operations. By accepting the guidelines set forth in the WPS and constantly looking for means to maximize procedures, fabricators can achieve higher effectiveness levels and exceptional end outcomes.
Ensuring Security in Manufacture
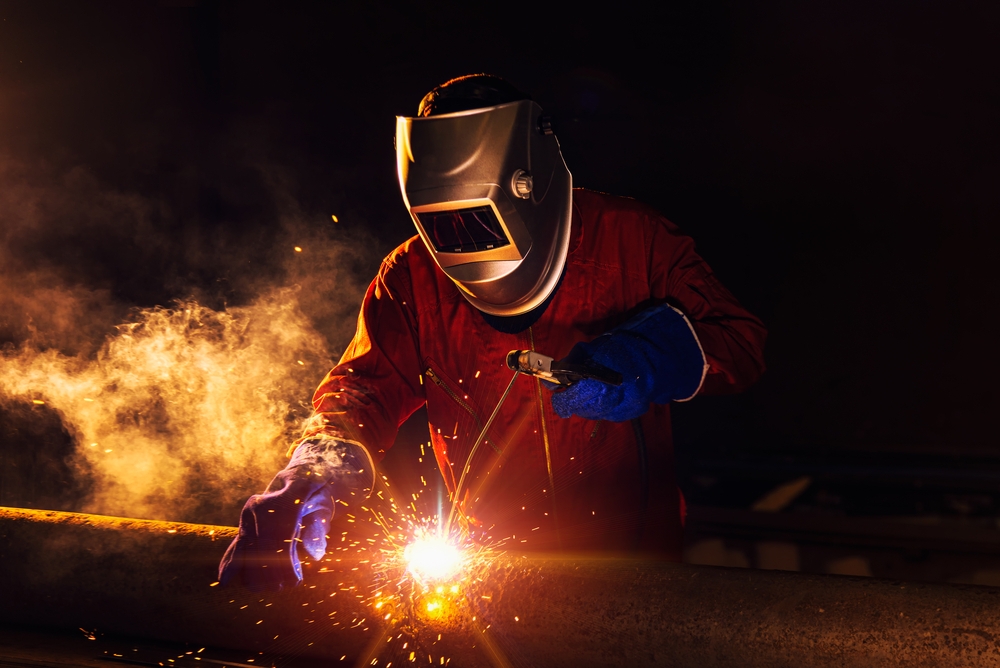
Making certain safety and security in fabrication entails a multifaceted strategy that encompasses numerous elements of the welding procedure. Welders should be furnished with ideal equipment such as helmets, news gloves, and protective clothes to alleviate risks connected with welding activities.
Additionally, adherence to correct air flow and fume removal systems is vital in keeping a healthy and balanced job setting. Welding fumes contain unsafe materials that, if breathed in, can posture significant wellness dangers. Carrying out efficient ventilation steps helps to minimize direct exposure to these unsafe fumes, promoting respiratory system health amongst employees.
Routine devices upkeep and evaluations are additionally important for guaranteeing security in manufacture. Damaged machinery can lead to injuries and crashes, highlighting the significance of prompt repair services and routine checks. By focusing on precaution and cultivating a society of recognition, construction centers can produce a effective and safe workplace for their workers.
Executing WPS Best Practices
To enhance functional performance and make sure high quality outcomes in manufacture processes, including Welding Procedure Requirements (WPS) finest methods is critical - welding WPS. Implementing WPS ideal techniques includes meticulous preparation, adherence to market criteria, and constant surveillance to guarantee ideal outcomes. First of all, picking the appropriate welding process, filler product, and preheat temperature defined in the WPS is critical for accomplishing the wanted weld quality. Second of all, making certain that qualified welders with the needed qualifications accomplish the welding treatments according to the WPS guidelines is crucial for consistency and integrity. Routinely upgrading and reviewing WPS files to show any type of process renovations or modifications in products is additionally a vital best practice to maintain precision and importance. Additionally, providing thorough training to welding personnel on WPS needs and best practices fosters a culture of safety and security and quality within the fabrication atmosphere. By diligently carrying out WPS ideal techniques, producers can streamline their operations, minimize errors, and deliver exceptional items to fulfill customer expectations.
Verdict
In conclusion, welding WPS plays an important role in ensuring efficiency and security in manufacture processes. By complying with these strategies, businesses can open the complete potential of welding WPS in their construction procedures.
In the realm of fabrication, Welding Treatment Specifications (WPS) stand as the foundation of welding procedures, determining the required steps for accomplishing both effectiveness and safety in the construction process. By specifying important specifications such as welding procedures, products, joint layouts, preheat temperatures, interpass temperature levels, filler metals, and post-weld warmth treatment requirements, WPS supply a standardized technique to welding that enhances performance, quality, and safety and security in fabrication procedures.

When maximizing welding procedures, leveraging the crucial aspects described in Welding Procedure Specs (WPS) comes to be essential for enhancing procedures and making the most of productivity. (welding WPS)
Report this page